The Ultimate Guide to Hydraulics Pumps: Maximize Efficiency and Performance
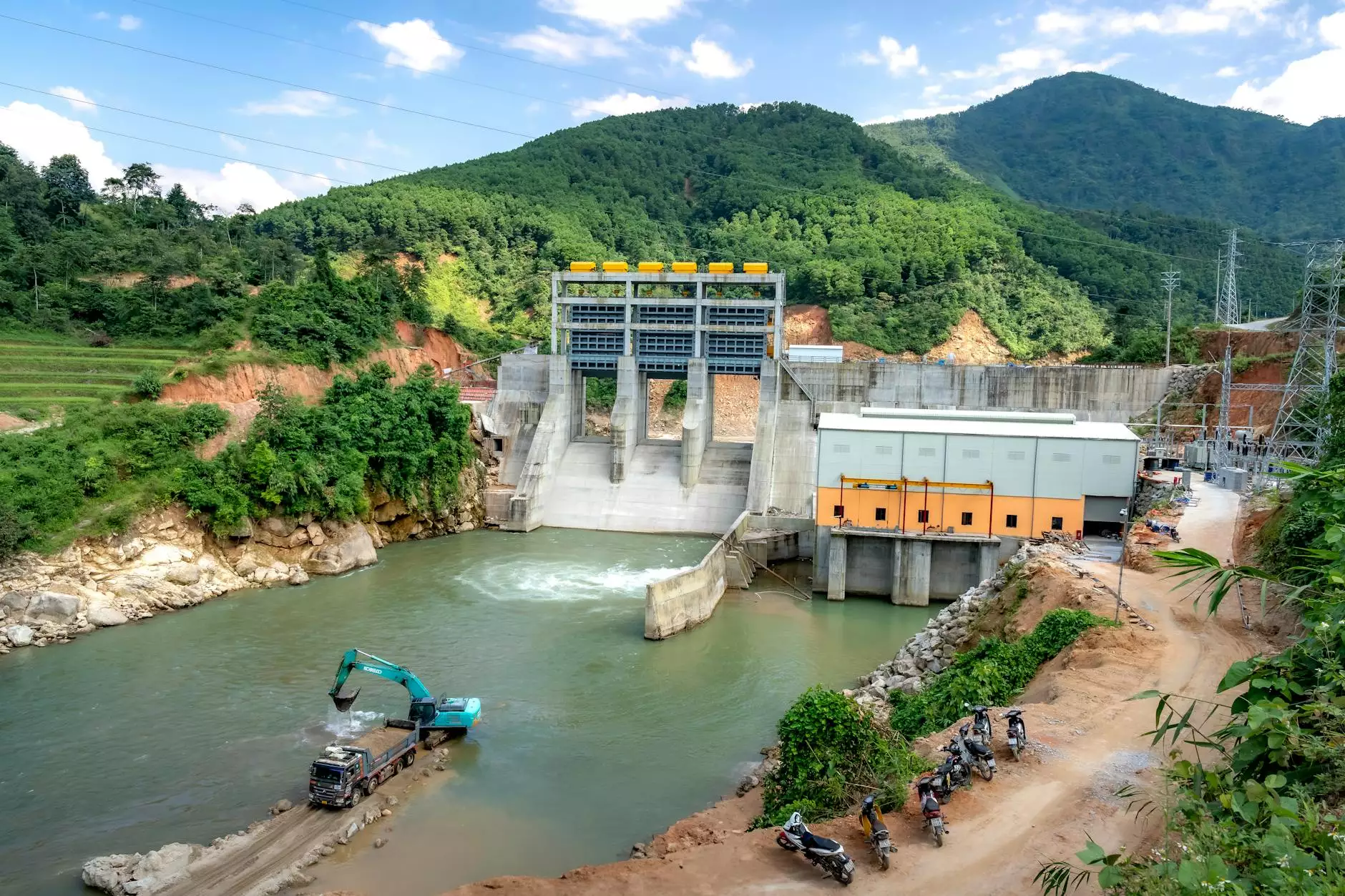
In today's highly competitive industrial landscape, the demand for efficient and reliable machinery has never been higher. One critical component that stands out in this regard is hydraulics pumps. These pumps play a pivotal role in various applications, from automotive industries to construction, making them indispensable. In this comprehensive guide, we will delve deep into the world of hydraulics pumps, exploring their types, functioning, applications, and much more. Whether you are a business owner or an enthusiast, this article will equip you with essential knowledge to leverage hydraulics effectively.
Understanding Hydraulics Pumps
At its core, a hydraulic pump is a mechanical device that converts mechanical energy into hydraulic energy. This energy is then utilized to move fluid, typically hydraulic oil, through a system. The primary function of these pumps is to create a flow of hydraulic fluid, which is used to power various machines and tools.
How Hydralics Pumps Work
The operation of a hydraulics pump hinges on the principles of fluid mechanics. When the pump is engaged, it creates a vacuum that draws fluid from a reservoir. This fluid then gets pressurized and directed through hoses and pipes into hydraulic cylinders or motors, which in turn perform the desired work.
Types of Hydraulics Pumps
There are several types of hydraulics pumps, and understanding the differences can help you choose the right one for your specific applications. Here are the main types:
- Gear Pumps: Commonly used in low-pressure applications, gear pumps use two gears to create flow. They are simple, reliable, and cost-effective.
- Vane Pumps: These pumps use a rotating mechanism with vanes to generate flow. They offer good efficiency and are suitable for medium-pressure applications.
- Piston Pumps: Known for their high efficiency, piston pumps use one or more pistons to create fluid flow. They are ideal for high-pressure applications.
- Peristaltic Pumps: These pumps utilize a rotating roller to compress a flexible tube, propelling fluid forward. They are excellent for pumping sensitive fluids.
Applications of Hydraulics Pumps
The applications of hydraulics pumps are vast and varied. Below, we explore some common areas where these pumps are utilized:
1. Automotive Industry
In the automotive sector, hydraulics pumps are essential for operating braking systems, power steering, and engine control systems. Their ability to deliver reliable power makes them indispensable in modern vehicles.
2. Construction
Construction machinery such as excavators, cranes, and loaders rely heavily on hydraulics pumps to lift and move heavy loads. The efficiency of hydraulic systems allows for precise control of equipment.
3. Manufacturing
In manufacturing, hydraulics pumps are used to power machines for cutting, molding, and stamping operations. Their high power-to-weight ratio makes them ideal for compact manufacturing setups.
4. Agricultural Equipment
Agricultural machinery such as tractors and harvesters utilize hydraulics pumps for various tasks, including lifting implements and adjusting equipment settings.
Benefits of Using Hydraulics Pumps
Investing in high-quality hydraulics pumps can provide numerous benefits, which include:
- Efficiency: Hydraulics systems are known for their efficiency, allowing for smaller systems to produce large amounts of power.
- Precision: Hydraulic systems offer high precision, making them suitable for applications requiring fine control.
- Safety: Hydraulics can operate under extreme conditions and reduce the risk of mechanical failures.
- Diverse Applications: The versatility of hydraulic systems means they can be tailored to numerous industrial applications.
Maintenance of Hydraulics Pumps
Proper maintenance of hydraulics pumps is crucial for ensuring their longevity and efficiency. Here are some essential maintenance tips:
Regular Inspection
Routine inspections can help identify leaks, wear, or damage in the hydraulic system. Ensure that all connections are tight and that there are no visible signs of fluid leakage.
Fluid Monitoring
Check the hydraulic fluid levels regularly and ensure that the fluid is clean. Used fluid can contain contaminants that may damage the system.
Filter Replacement
Hydraulic fluid filters should be replaced periodically to prevent contamination from entering the system, which can lead to pump failure.
Temperature Management
Monitor the operating temperature of the hydraulic system, as excessive heat can lead to fluid breakdown and performance issues.
Choosing the Right Hydraulics Pumps
Selecting the right hydraulics pumps is essential for achieving optimal performance in your application. Here are some factors to consider:
- Application Requirements: Understand the specific requirements of your application, including flow rate and pressure.
- Fluid Type: Choose pumps compatible with the type of hydraulic fluid you are using.
- Brand Reputation: Opt for pumps from reputable manufacturers to ensure quality and reliability.
- Cost vs. Quality: Balance your budget with the need for performance and durability—cheaper pumps may not last as long.
Conclusion
In summary, hydraulics pumps are an integral part of many industries, providing the power needed for efficient machinery operation. Understanding their types, applications, maintenance requirements, and selection criteria is crucial for any business relying on hydraulic systems. If you are looking to enhance your operations, consider investing in high-quality hydraulic pumps and maintain them diligently for optimal performance. Explore our extensive range of hydraulics pumps and related products at shophydraulicamerica.com and take your business to the next level.